Machines and systems in the food industry must function perfectly even under extreme conditions of use. Dampness, contamination, high temperatures and high relative humidity stress the parts of the system and have a considerable adverse effect on the working life of bearings and chains. In most cases in the food industry, this involves mass production systems, where any downtime means high production losses. Even in modern beverage plants, chain or conveyor systems are in operation 24 hours a day and continuous lubrication extends their reliability and service life enormously.
Challenges | Solution |
---|---|
High demands on the durability of the products | Simalube with H1 approved lubricants for the food industry |
The use of approved special lubricants requires a flexible product | Special accessories for the food industry |
Usage partly in dust explosion hazardous areas (ATEX) | Simalube lubricant dispensers are approved in all ATEX areas |
Areas of application and advantages
Typical installations | Typical applications | Further benefits |
---|---|---|
Conveyor belts | Bearings | Increased operational safety |
Palletizing systems | Chains | Reduced downtime |
Presses | Guides | Constant supply of hard to reach lubrication points |
Washing machines | Gears | Less time spent on maintenance |
Packaging machines | Reduction of wear and longer life of the components | |
Processing machines | ||
Ventilators / Fans | ||
Conveyor systems |
Simalube applications in the food industry | Simalube applications in the beverage industry | Benefits from automatic lubrication with simalube |
---|---|---|
Preparation processes (peeling, grinding, pressing, cutting machines) | Filling machines | Reduction in servicing and maintenance: no more lubrication by hand, this results in enormous savings of time costs |
Processing operations (washing units, cooling and freezing units) | Washing machines | It is not necessary to switch the machines off while they are being serviced |
Filling and loading processes (conveyor systems, slicers, filling systems) | Belt conveyors | Longer service life of machines thanks to continuous and precise lubrication |
Packing machines (packing, shrink-wrapping labelling) | Packaging and shrink-wrap machines | Flexibility: The running time is adjustable from 1–12 months |
Palletizers | Presses | Only one type of lubricator is needed per application. This allows a reduction of storage costs |
Refrigeration and freezer units | ||
Label machines | ||
Palletiser | ||
Air conditioners (facility management) |
Sold millions of times and suitable for any single point lubrication task with grease or oil.
The automatic lubricator simalube provides all possible kinds of lubrication points with lubricant. 24 hours, day in, day out.
Roller bearings which are not lubricated sufficiently or wrongly drop out long before they have reached their expected product life. Simalube lubricators guarantee a consistent supply of lubricant in the pre-adjusted proportioning. Shutdown times are decreased and costs in comparison to time-consuming lubrication by hand are clearly reduced
Within seconds simalube is fixed to the lubricating point. On commissioning, a gas production cell is activated which presses the lubricant on the lubrication point through the release of hydrogen gas. The lubrication amount can be steplessly adjusted by means of an Allen key.
Filled with oil, Simalube is applied for the automatic lubrication of chains, open gears or guide rails for example.
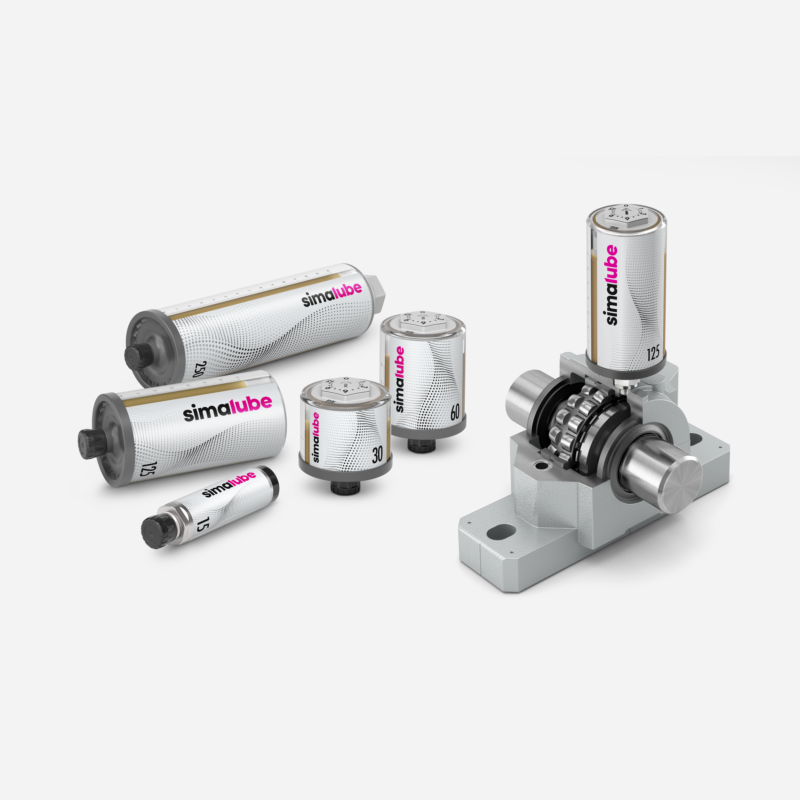